An intrepid new robot could prevent deaths in the oil and gas sector by carrying out inspections in hazardous areas that workers would otherwise have to do. its creators have said.
The government-funded National Physical Laboratory and Ross Robotics unveiled the system at an NPL relaunch event at its headquarters in Teddington. south-west London.
Engineers showcased the autonomous robot and inspection software side-by-side ahead of plans to combine the two for commercial application. “Hopefully small firms will see it. take it on and think of innovative ways of using it.“ said Matthew Maynard. head of advanced manufacturing at NPL. the UK’s national measurement institute. “There is so much good science here and we are trying to make sure it has the impact it needs.“
In the past 10 years. 22 people have died in accidents during inspections of hazardous oil and gas facilities in the UK. The developers hope the robotic system will help eliminate risk. while also providing greater accuracy and more objective results.The NPL software uses highly accurate ‘digital image correlation’ technology to spot cracks and faults in structures. Engineers tested the system by scanning 25m of a railway tunnel. the cameras taking 11 24-megapixel photos every metre with a resolution of one pixel per millimetre – reduced from an ultimate resolution of 0.05mm owing to environmental factors such as vibrations and atmospheric conditions.Combined with simultaneous localisation and mapping (Slam) technology. which keeps an exact track of where the robot is at all times. the software allows engineers to automatically check for structural changes to an accuracy of 1mm by superimposing two scans and looking for differences pixel-by-pixel.
The technique should help eliminate human error. said NPL developer Nick McCormick. “A lot of these things sound like optional extras. but when you start doing it in reality you need a lot of sophisticated software.“ he said.
The mid-size Ross Robotics 2.0 platform will host the NPL camera system and software. The caterpillar-track droid uses a modular design. allowing users to “pull it apart and stick it together again.“ according to Ross’s research and development director Philip Norman.The robot is designed for reliability and ease-of-use. automatically adapting to changing environments but still returning to base using the Slam technology. Engineers and scientists at the CERN particle physics laboratory in Geneva have tested and used the platform for inspections around the Large Hadron Collider. where strong magnetic fields and radiation create hostile environments.
The system developers hope it could also be adapted for inspection drones. The digital image correlation technology offers better resolution than similar lidar scans. they say. and does not rely on visible targets needed for photogrammetry.
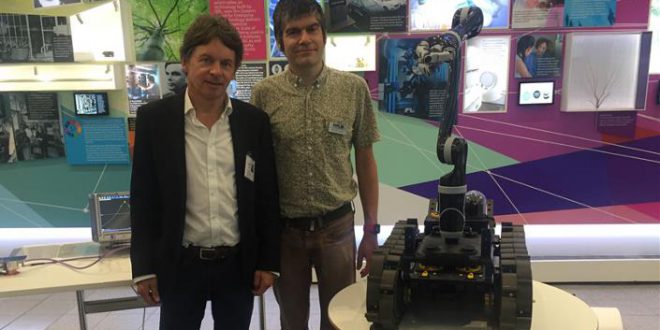