Fleischanderl’s passion for improving and developing the sector is tangible, an important attribute as hard-to-abate sectors struggle to keep up with global emissions targets.
Primetals is a global plant engineering company catering for the steel sector and a member of the Mitsubishi Heavy Industries (MHI) Group. Primetals was recently in the news with the launch of their Hydrogen-based fine-ore reduction (HYFOR) pilot plant at the Voestalpine According to Primetals, roughly 1.8 tonnes of CO2 are released into the atmosphere for every tonne of liquid steel produced on the still predominant, integrated process route — which relies on coking coal as its main energy source. This estimate is conservative as many plants around the world emit three or more tonnes of CO2 per tonne of steel, resulting in total emissions that amount to 7–10% of global greenhouse gas output.
Fleischanderl explains the process of producing steel, as well as the importance of direct reduction to achieve the net-zero target. He highlights that there are three ways to reduce iron ore oxides from the mines to iron process: by using carbon from fossil fuels; hydrogen; or electrons (electrolysis). Alternatively, old scrap can be re-melted in an electric furnace which is a low-emission alternative, but hampered by a global scarcity of scrap.
“Pelletizing beneficiated ores is the dominant way to produce steel via a coking plant and blast furnace,” says Fleischanderl.
“Direct reduction plants today are based on natural gas, which already has a potential to decarbonize by 50% compared to the blast furnace route, however, this is just an intermediate goal. If we want to achieve net carbon zero by latest 2050, we need to replace natural gas with low carbon hydrogen. This is where HYFOR comes in.”
The HYFOR project, which was first announced by Primetals Technologies in 2019, has now moved from lab-scale testing to the pilot-plant stage.
Fleischanderl states that the lab scale “included a lot of simulation work on direct reduction with various technologies, as well as working on fluidized bed technology. Based on these data we designed the pilot plant. Ultimately, our intention is to move toward an industrial-scale plant in a stepwise fashion.”
The Austrian-based pilot plant was partially funded by the Austrian government. The project completed the first successful tests on different types of iron ores and will now begin to perfect the process and will be ready for building an industrial prototype plant within two years.
Unlike conventional direct reduction plants (such as those based on the Midrex process, which can also be run on 100% hydrogen), HYFOR is based on fluidized-bed technology — making it possible to use iron-ore fines directly, without having to pelletize the material first.
The final product from the HYFOR process is sponge iron (DRI/HBI), which can be easily shipped long-distance and used as feedstock to make steel in electric arc furnaces at low carbon intensity or fed into conventional blast furnaces to lower the use of coking coal.
Since HYFOR can operate on iron ore fines without much pre-processing, the process is especially well suited for deployment in regions that are rich in low-grade iron ore and have the potential for large-scale renewable energy production from solar and wind — core requirement for zero-carbon hydrogen production.
After succeeding with the lab scale, Fleischanderl explains that the team came to a point where they had to decide whether or not to invest in a pilot stage. “The green light was given and the pilot was commissioned in April this year, and since May, the team are running the first campaigns. So we’re really, really happy”.
“We are still optimizing the plant, but we can clearly say the plant works. We are running the reduction campaigns on 100% hydrogen, so not utilizing any fossil fuel for the reduction process. Only hydrogen plus electric energy.”
Fleischanderl says that they are already looking forward to the next stage, which is to build the industrial prototype, decide on collaboration partners and scale up engineering.
“A fully commercialized plant runs up to 250 tonnes [of DRI/HBI] per hour, so this still requires a scale up factor of 15, which is our ultimate goal. All in all, perhaps we can start the commercialization phase in 2025.”
When it comes to decarbonizing the steel sector, Fleischanderl highlights that large investments into assets will be needed to ensure there is enough steel produced to meet growing demand, while significantly lowering emissions.
“In 2050 we will see much more than 2 billion tonnes of steel produced, giving rise to more material efficiency initiatives. Hydrogen and CCUS are the most promising technologies at the moment, although developing that will take time.”
Primetals is also involved in other innovation. They are invested in a US biotech company that uses microbes to ferment carbon-rich waste gases into base chemicals, such as bio ethanol.
Another technology the team is investigating utilizes by-products such as slag to decarbonize the cement industry, while also recovering energy from waste heat. And yet another innovation, Arvedi ESP, directly links the casting and rolling of steel, avoiding the need to re-heat slabs and saving up to 40% of carbon emissions in the process.
Fleischanderl concludes: “I truly believe that hydrogen should first serve sectors like steel, rather than using it to power vehicles, for example.
“In our industry, one tonne of hydrogen can abate up to 26 tonnes of CO2 emssions — with transport applications, that’s only 6 tonnes. It’s never black and white, but I think hydrogen’s starting place is to decarbonize hard-to-abate industries, providing greater benefit to our world.”
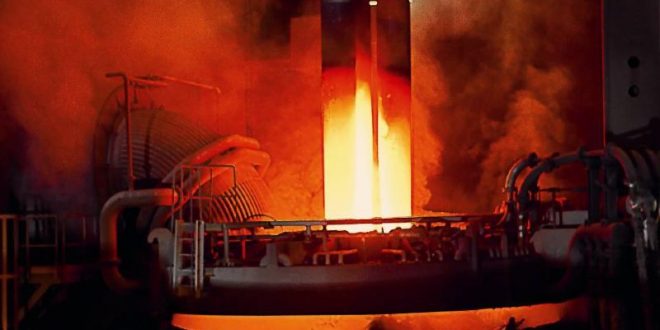